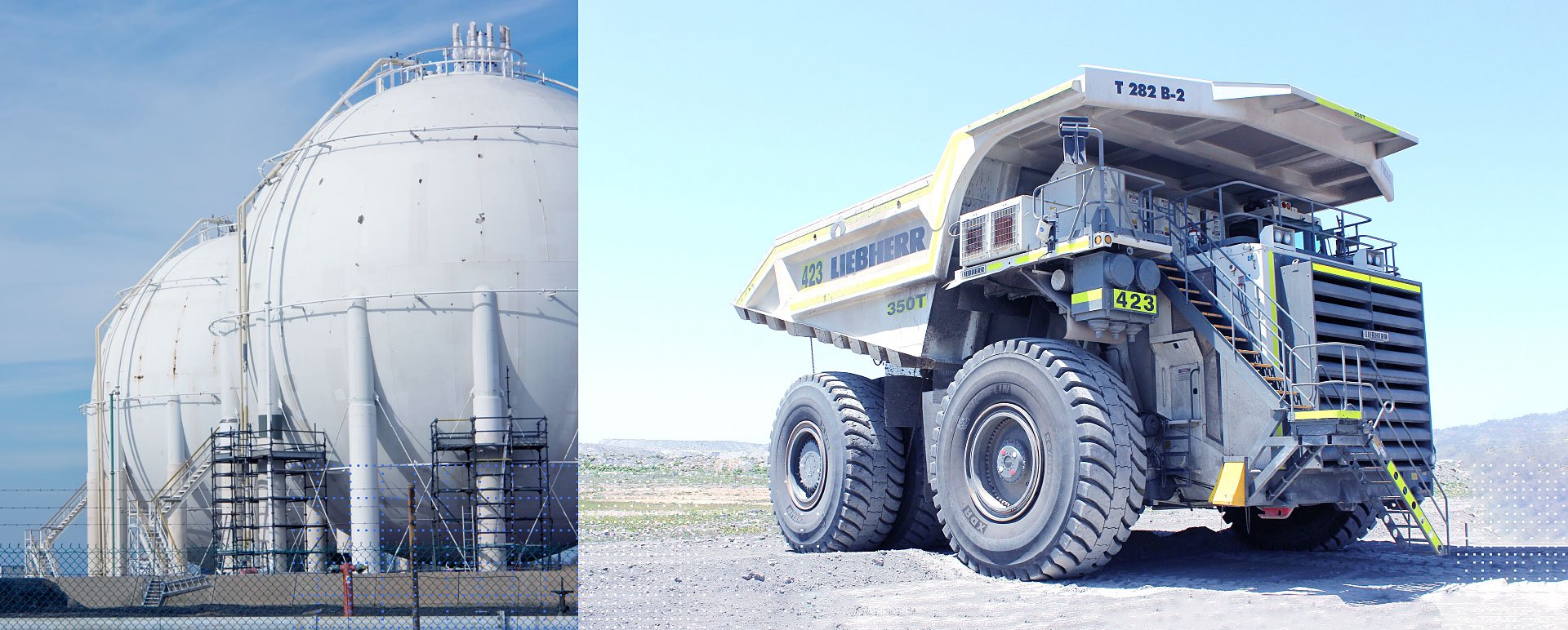
Resources, Oil and Gas
ASSET EXPERIENCE
Trucks
Ancillary
Digging Units
Materials Handling
Fixed Plant
Underground
Drill & Blast
Load & Haul
Conveyor & Stockpile
Inventory, Warehouse & Parts Management
Processing
Improving Shutdowns & Turnarounds
Enabling ERP Transformation
Maintenance & Asset Management Frameworks
Supply Chain & Supplier Development
Frontline Leadership & Business Improvement Training
The dynamic operating environment of this sector presents both risk and opportunity. We develop strategies that allow operators to better navigate this environment and improve return on investment. We also provide expert advice and comprehensive support to enhance safety, security and productivity, and deliver impressive cost savings.
Our team has significant expertise across the full breadth of mining operations – including engineering, mine management, logistics and maintenance. It gives us a strategic lens through which we identify opportunities and deliver sustainable multifaceted, transformational improvements to work environments, processes and outcomes.
But our support goes beyond spreadsheets and boardroom briefings. We use advanced simulation, mathematical modelling and regular onsite engagement to accurately assess challenges and develop precise solutions that have real-world applicability.
We work closely with the resources, oil and gas industry to embed sustainable processes which define clear responsibilities, reduce complexity and prevent costly errors.
Using advanced analysis techniques, we provide a more accurate assessment of issues and tailor appropriate solutions that increase productivity and production of hydrocarbons, and ensure adherence to tight schedules and budgets.
DELIVERABLES
Managing complexities in underground mining
Our team understands the importance of managing complexities in the unique environment of underground mining. We utilise advanced technical experience from various industries – including automotive and manufacturing – to apply innovative approaches that improve precision, mitigate risks and reduce bottlenecks.
Optimising port and rail operations
Secora uses highly-specified tools and tailored methodologies to streamline port and rail operations for the mining industry. Our mathematical simulations and capacity modelling enable us to analyse complex systems, pinpoint constraints and provide tested solutions that reduce shutdown times and manage outages.
Leveraging digital transformation
We help businesses to adapt and grow through digital transformation. We assist them to adopt innovative technologies and digital solutions that deliver efficiencies, increase productivity, and strengthen protections against vulnerabilities like cybercrime.
Mitigating external risk
We understand the need for the industry to manage and plan for rapid changes in external factors, including fluctuations in commodity prices for instance. We use mathematical simulation and modelling to inform planning and assess and mitigate risk. This also enables businesses to track infrastructure capacity, inventory trends and performance to ensure alignment.
Implementing standardised processes
Secora implements standardised processes which establish accountability and transparency, enhance supply-chain management and foster a high-performance culture in workplaces. This creates efficiencies and reduces the risk of mistakes for companies as they navigate an evolving industry.
Embedding best practice for health and safety
We put safety at the forefront of our work across the oil and gas industry, noting the potential for significant harm to individuals, businesses, communities and the environment if this is compromised. We assesses the health and safety implications for any proposed change, and ensure that improvements in safety, profitability and organisational performance are felt simultaneously.
SAMPLE RESULTS #1
The three plant shutdowns during the project period were delivered as planned, delivering $13m in direct benefits based on the elimination of consistent overruns.
SAMPLE RESULTS #2
Reduction of all ITC service types delivered savings of 2,058 resource hours per year; the elimination of water tank swap out eliminated high risk activity and saved 624 resource hours per year
CLIENTS
AngloAmerican
Barrick Gold
BHP
BMA
BP
Dalrymple Bay Coal Terminal
ExxonMobil
FMG
Glencore
Newcastle Coal Infrastructure Group
Newcrest
Oil Search
Origin
Petronas (Malaysia)
PetroVietnam
Pertamina (Indonesia)
Rio Tinto
Shell
South32
Woodside
Yancoal
READ CASE STUDY